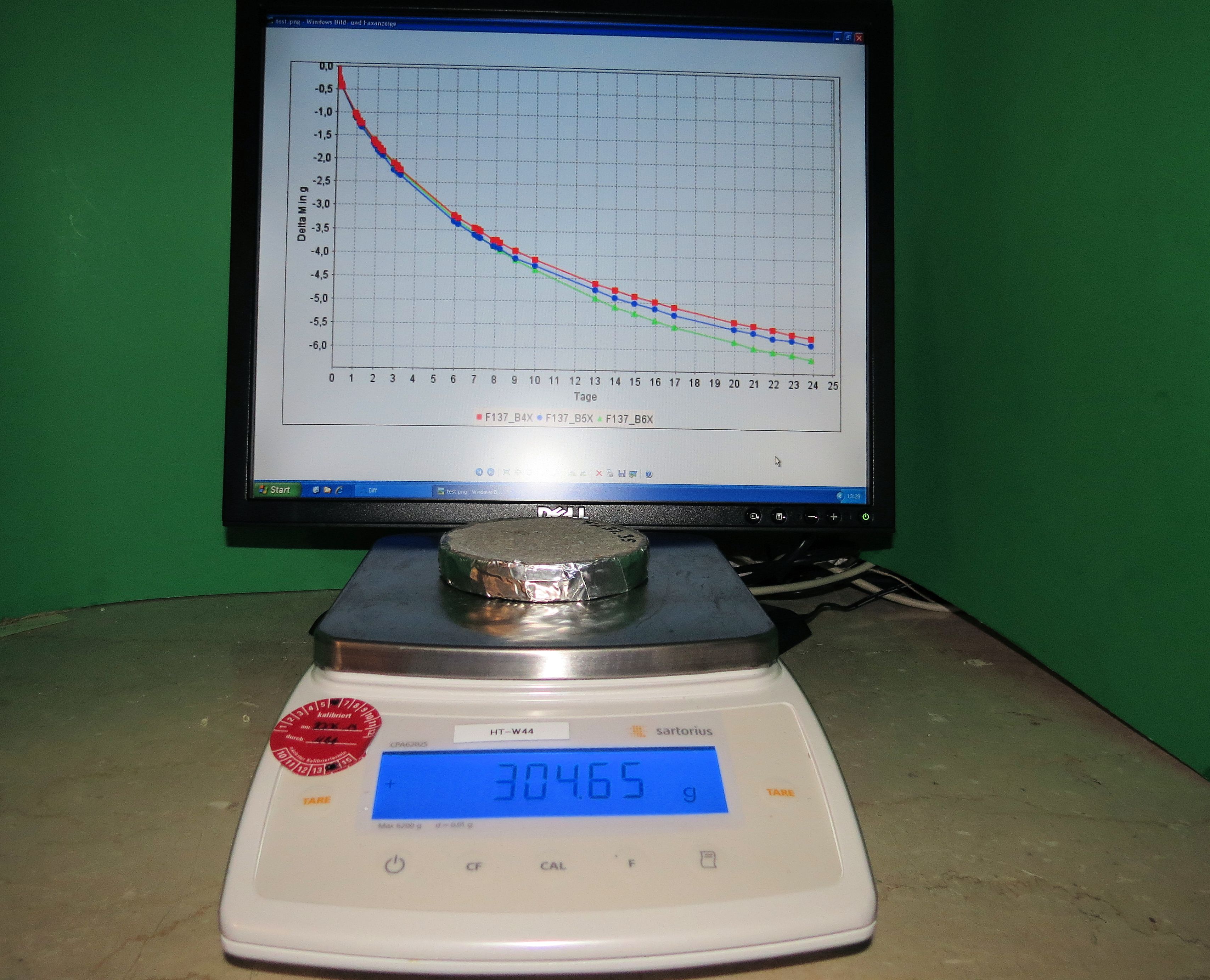
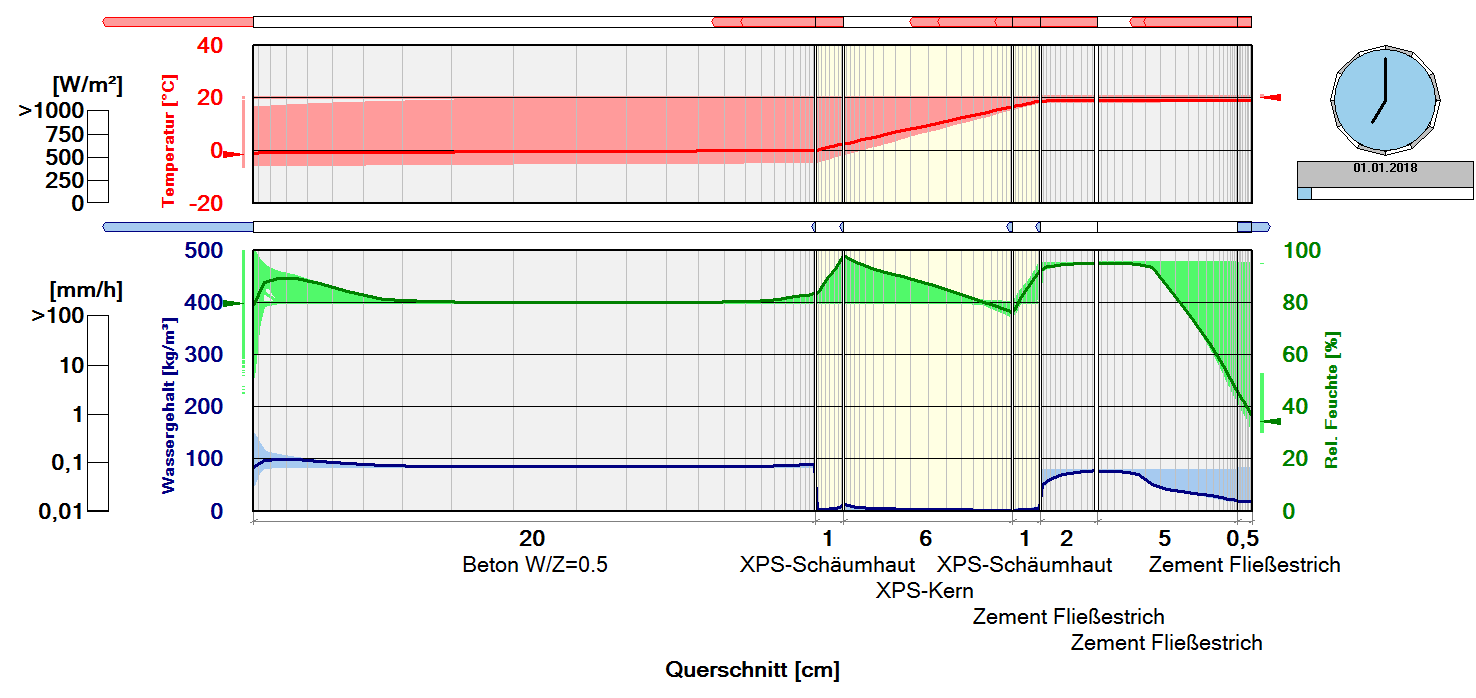
In most cases where water damage occurs in buildings, floors are affected the most. Standing water on the surface seeps into the underlying screed, which quickly becomes saturated if the surface water is not removed immediately. Before a new floor covering can be laid and the building can be used as before, the screed has to be dried or replaced. To determine the drying rates of diverse screed products, researchers at Fraunhofer IBP have conducted numerous laboratory tests to establish their material characteristics and drying behavior. The findings of these tests make it possible to calculate the drying-rate curves for these types of screed and the time required for them to dry.
Floor screeds have a high water content after they have just been laid or after water damage. This can lead to high humidity levels indoors and to the growth of mold on surfaces and in cavities. Wet screed therefore needs to be dried before a new floor covering is laid and the building can be reused. The drying rate depends not only on the drying method but especially on the type of screed product employed. To predict the drying-rate curve and drying time for different types of screed, various material characteristics were determined in the laboratory and drying tests were carried out on the screed products.
The tests were conducted on commonly-used anhydrite screeds and flowing cement screeds. Each type of screed was prepared using different proportions of additives and binders. Depending on the composition of the screed, the results showed that the drying time varied considerably between anything from 4 weeks to six months.
It was also observed that material properties differed depending on the thickness of the screed. For example, fine particles present in the mixture could rise to the surface and form a thin film that inhibited the drying process. A sedimentation process was also observed in which the mixture sometimes separated into multiple layers, each with different characteristics. For this reason, the screed samples were tested layer by layer and material properties were determined separately for each layer. This dependency on thickness must also be taken into account in mathematical calculations.
Using the knowledge thus obtained and the material properties ascertained, the researchers can now simulate the drying behavior of specific types of screed under a wide range of conditions with the aid of hygrothermal simulation programs. If the composition of the screed is known, more precise tests can be performed to assess the methods employed to accelerate the drying process.