Aiding the drying process of interior building structures
Water damage caused by burst pipes or flooding is never easy to deal with. Apart from the inconvenience (and cost) of having to replace damaged furniture, it can also have more serious consequences. Water infiltrating into the structural elements of a building such as floors, walls and ceilings can affect their stability and reduce their thermal insulation properties. The increased humidity also encourages mold growth.
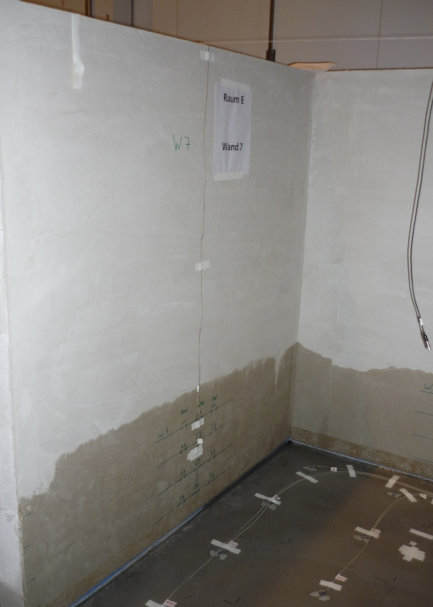

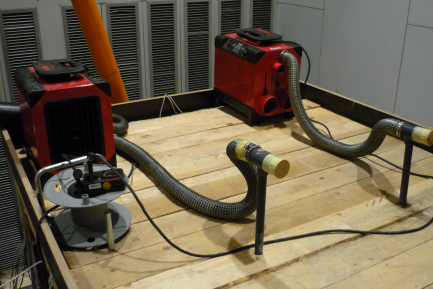
In Germany, insurance companies process on average 3000 claims for water damage every single day, or up to 1.1 million cases a year, resulting in annual compensation costs of around 2 billion euros (source: GDV). Typical causes of water damage include old leaky pipes, burst pipes due to the freeze-thaw cycle, and badly-installed plumbing. All too often, the problem goes unnoticed for quite some time and only becomes visible when damp patches start to appear on the wall or ceiling, or when water forms puddles on the floor. By this stage, the dampness may have already spread to other parts of the building. Extreme weather conditions with heavy rainfall and flooding can also cause substantial water damage to buildings. Another source of damp that is typically encountered in newly-built homes is the residual moisture in building materials such as floor screeds, wall plaster and concrete, which contain large quantities of water when they are applied.
It is therefore all the more important to understand and be able to evaluate how water infiltration affects the hygrothermal behavior of building materials and building components. Only then can effective drying methods be developed to restore them to their original state after flooding or other types of water damage. Companies that specialize in dealing with damp are increasingly facing new challenges due to the diversity of building materials used in all possible combinations – including vertical-core blocks with and without integrated insulation, solid bricks, aerated concrete blocks, and different types of damp-proof membrane. In order to obtain optimal drying results without the excessive use of energy, wide-ranging expert knowledge is required to choose the right treatment method in each case.
In recent years, the Fraunhofer Institute for Building Physics IBP in Stuttgart has carried out a large number of experimental tests to investigate the drying behavior of wall, floor and ceiling structures with artificially-induced water damage. A large climate simulator in the institute's laboratory complex in Stuttgart provides the ideal conditions for such tests. With a chamber measuring seven meters in length, six meters in width, and six meters in height, it can accommodate a wide range of components, including complete building shells, roof structures and individual test setups. The controlled environment enables optimal ambient conditions to be maintained during the tests.
On behalf of industrial customers, researchers from the institute's Hygrothermics Department have investigated the drying behavior of numerous construction materials and building components. To conduct many of these tests, they built complete rooms consisting of different types of floor, wall and ceiling structures. For instance, a floor might be made of a concrete slab, an insulating layer of a material such as EPS, mineral wool or perlite, and a top layer of screed. Materials used to construct the walls included vertical-core blocks with and without integrated insulation, aerated concrete blocks, gypsum wallboards, solid bricks, and lightweight wall panels, either with or without a tiled or plaster finish. In other experiments, the researchers investigated the drying behavior of ceiling structures consisting of wooden beams and planks with an insulating system of clinker or clay pellets. The test setups were equipped with a multitude of measurement sensors to track every detail of the water infiltration and drying processes. Various humidity and temperature sensors were installed in the flooring layers, inside the walls and ceiling structures, and also used to monitor the ambient air. Before starting the actual experiments, the setups were inundated with water for several days to artificially induce the effect of water damage for the purposes of simulation. In the case of wall and floor structures, the water was introduced at floor level (Fig. 1); for ceiling structures, water was introduced from above. This was followed by a drying period lasting several weeks. In some experiments to investigate drying behavior, the test setups were left to dry out naturally at a constant temperature and relative humidity in the climate simulator. In other experiments, different types of specialized drying equipment were used to assist the drying process.
These included, for example, sub-screed drying systems with adsorption dryers, infrared heating panels to dry walls, floors and ceilings, and adsorption dryers placed directly between walls and plastic sheeting (Fig. 2). To speed up the drying process for ceilings made from wooden planks, turbines were used to create a negative pressure between the joins (Fig. 3). Mechanical drying processes were tested both in continuous mode and with alternating on/off intervals. The results of some of the tests carried out in the laboratory were verified using the WUFI® simulation tool, which computes the coupled heat and moisture transfer in building components.
The measured data enabled the researchers to acquire extensive knowledge about the drying behavior of different test setups and materials in connection with various drying methods. By using different types of sensors, a detailed analysis of the drying rates of different structural layers could be made, allowing the drying method to be adapted accordingly. The results made it possible to evaluate the efficiency of the various drying processes and optimize the choice of suitable drying methods. It was also found that, in some cases, an alternation between natural and assisted drying produced the best results. The experimental setups were also checked for the possible development of mold.
The lab facilities available to researchers at the Fraunhofer Institute for Building Physics IBP and their in-depth knowledge of the drying behavior of building materials are a great asset when it comes to testing and evaluating different drying methods for complex structures made of multiple components. By simulating many different structures and drying methods, supplemented by mathematical simulations using the WUFI® software tool, drying behavior and the duration of the drying process can be predicted for each individual case.