Sound absorbers for aggressive flue gas media
Oil or gas heating systems make your home comfortably warm - and now even in a very energy-saving way. This clearly shows that considerable progress could be achieved with regard to the thermal efficiency of heat generators. However, they have become louder as a result, and the exhaust gas temperature of condensing boilers also causes significantly more condensate.
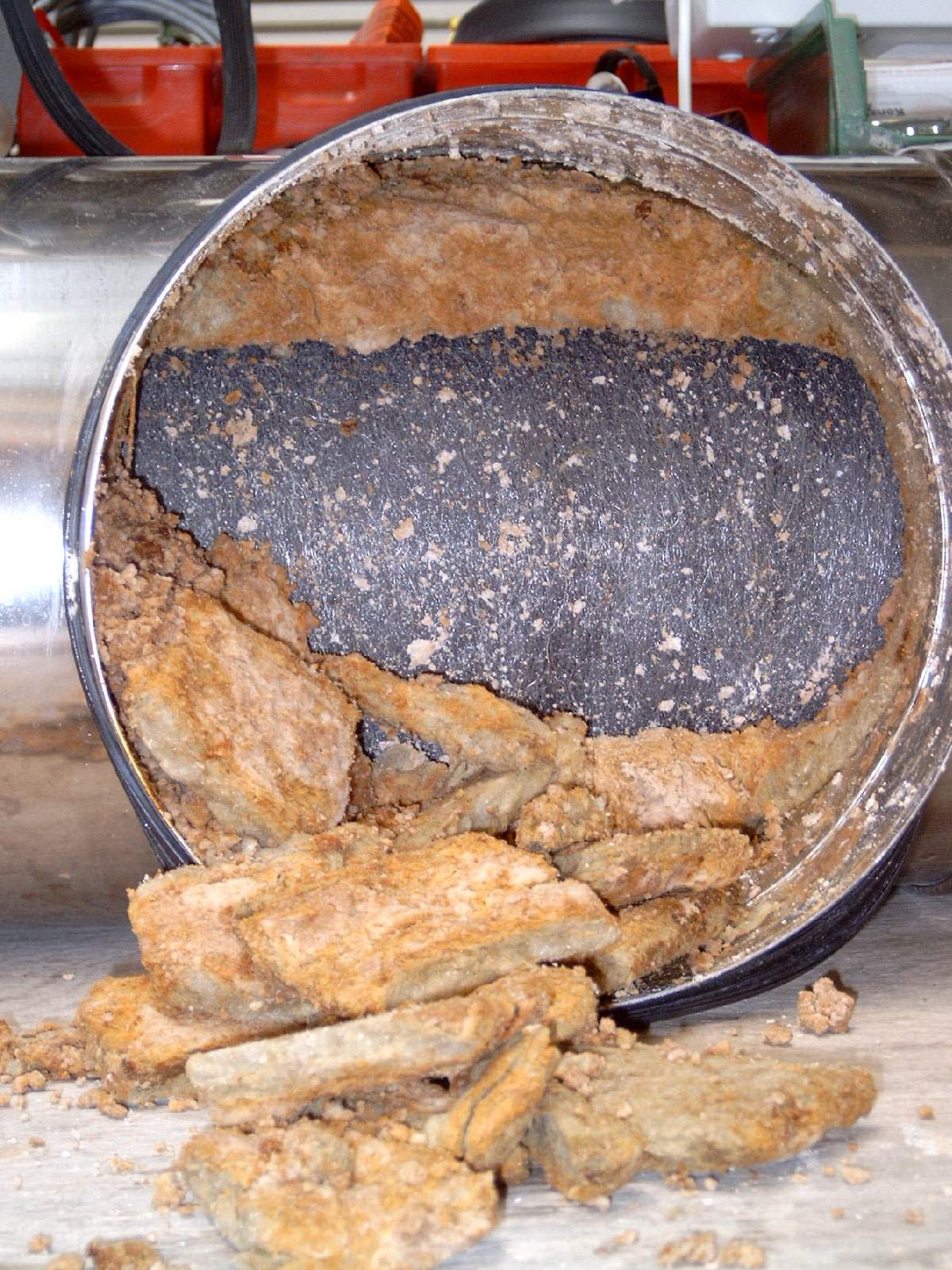
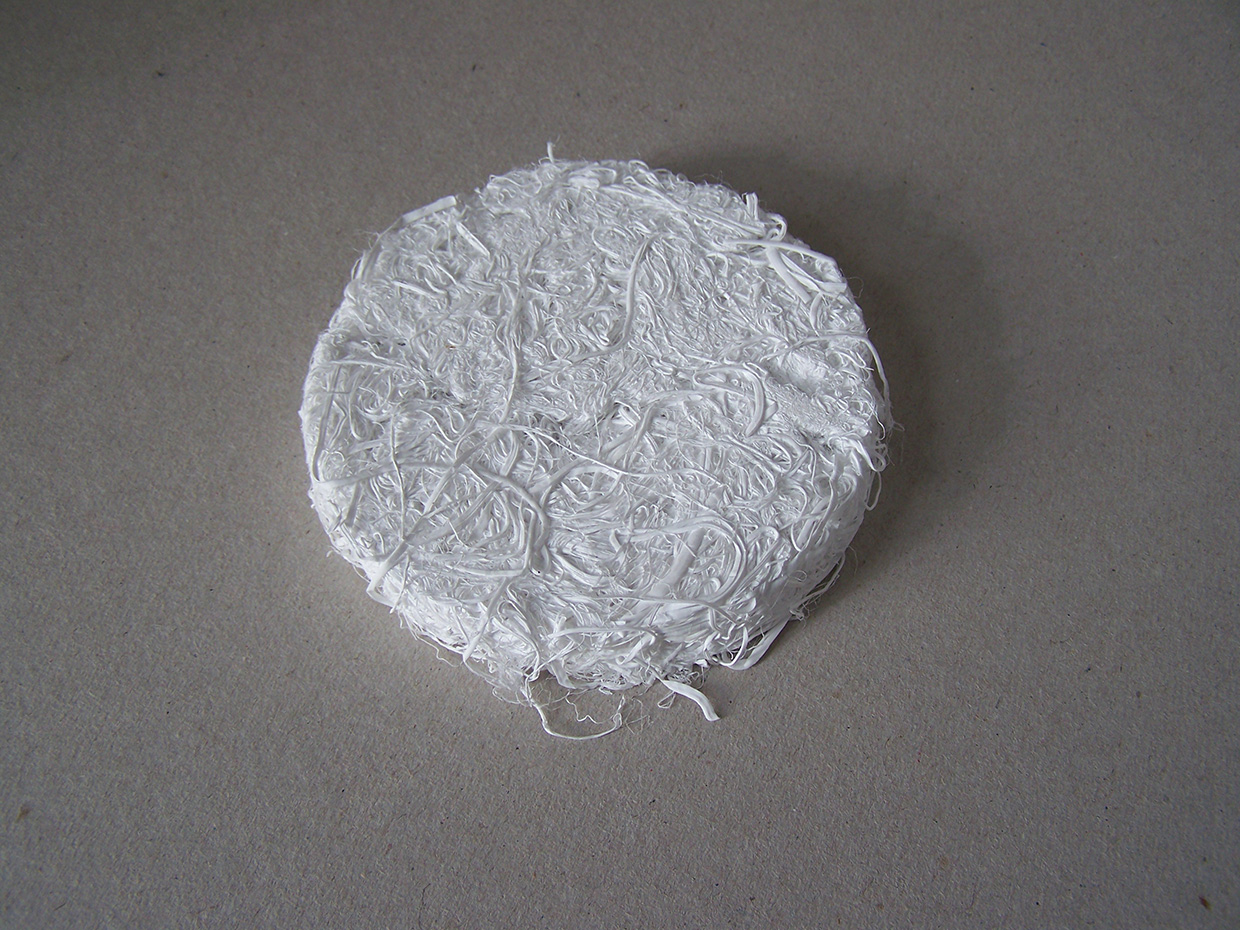
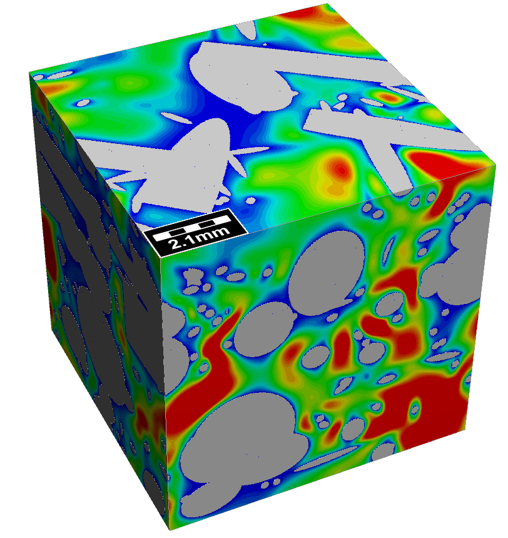
Condensate destroys the absorber
Most exhaust silencers used in heating systems are filled with porous absorber materials, such as mineral fibers. The capillary, open-cell structure "swallows", i.e., absorbs the sound. The drawback: condensate can also penetrate into these pores. As a result, the sound absorber can no longer perform its actual task. The absorber material is destroyed and must be disposed of as hazardous waste.
Absorber made of PTFE - better known as Teflon
Researchers at the Fraunhofer IBP have replaced the condensate-sensitive materials with unavoidable waste from PTFE production (commonly known as Teflon). The research project is funded by the Bavarian Research Foundation. In this approach, the scientists achieve sustainability in three respects: waste is recycled, new products are created that meet the requirements, and hazardous waste is avoided. The research team developed, in collaboration with the industrial partners KWO and Kutzner + Weber, procedures to create new sound absorbers from PTFE tapes with a fiber-like structure.
Production, advantages and areas of application
PTFE, like the raw material for mineral wool, initially has no acoustic properties. It only acquires these properties when it is processed in the form of fibers or granules and used in a composite. Since the starting material for PTFE products is very expensive, the researchers use a selection of suitable low-cost waste products and existing procedures for processing. Tapes made of PTFE meet these requirements due to their material structure, which allows them to be processed into fibers using rotating steel brushes or needle rollers. Further processing of these fibers results in variable but stable fiber composites that are suitable to be used as sound absorbers. Using model calculations and measurements on sample constructions, the scientists were able to demonstrate that the desired goal can thus be achieved: The resulting materials absorb sound in a broadband range and attenuate it in the medium and high-frequency range. These properties are retained even if the material is mechanically cleaned and reused. Accordingly, the material can be used permanently even under adverse conditions. The researchers first intend to use the new sound absorbers in aggressive exhaust media. However, the silencers also offer great potential in other market areas such as medical technology and the food industry, where chemical neutrality and resistance are also very important. And which sound absorber can survive a full washing cycle at 90 °C without damage and then be reused?